Exploring the Lathe Machine with Parts: A Comprehensive Guide for Metal Fabricators
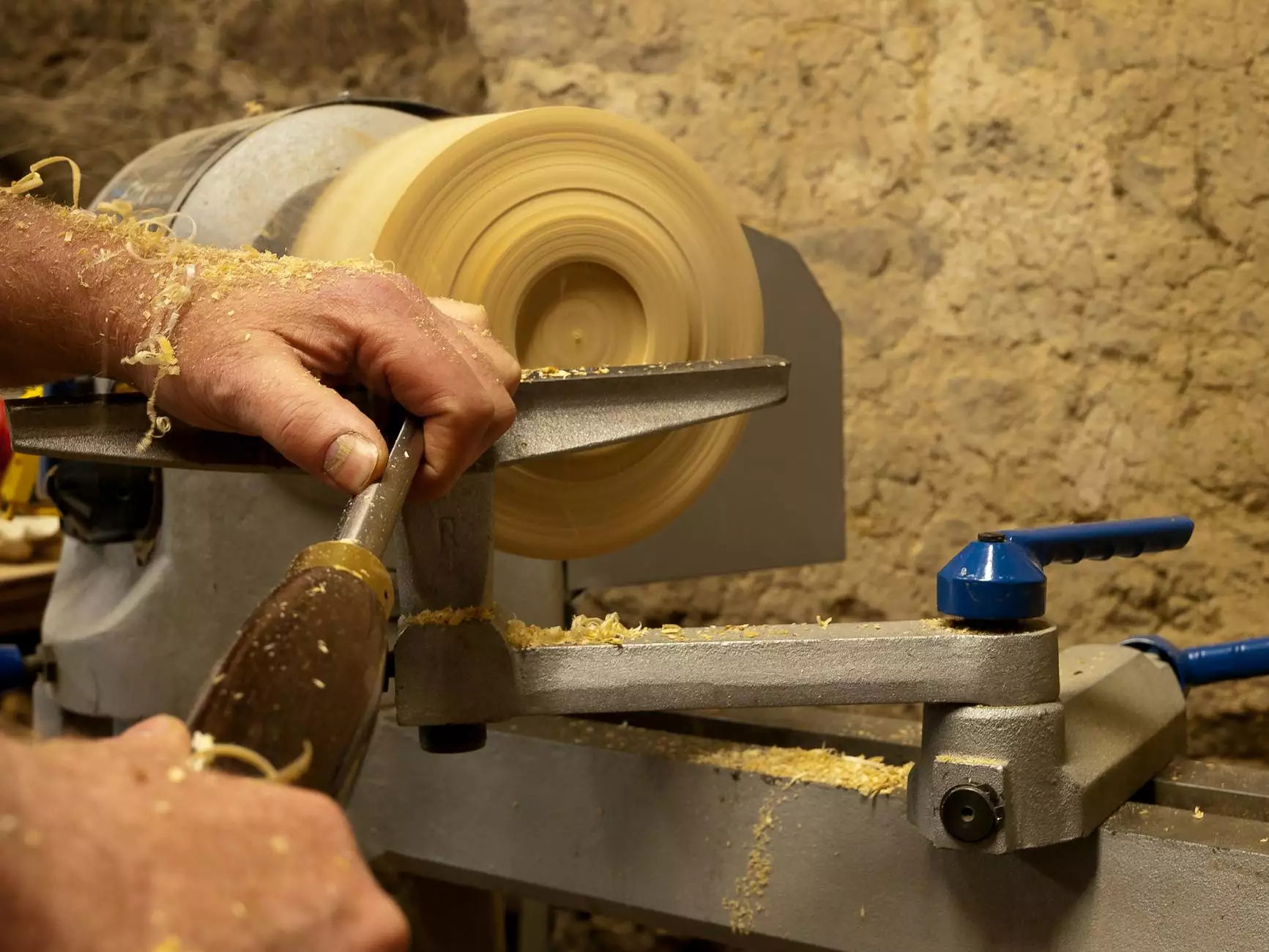
The lathe machine is an indispensable tool in the realm of metal fabrication. Renowned for its versatility and precision, it plays a pivotal role in shaping and machining various materials. For businesses engaging in metal fabrication, understanding the components and functionalities of the lathe machine is crucial. This article delves into the intricate details of the lathe machine with parts, ensuring you have the knowledge needed to optimize its use in your operations.
What is a Lathe Machine?
A lathe machine is a powerful tool used to cut, shape, and finish workpieces, primarily metals. It operates on the principle of rotating the workpiece against a cutting tool. This rotating mechanism allows for various machining processes, including turning, drilling, and threading. The versatility of the lathe makes it a staple in workshops and factories, especially in sectors focused on precision engineering.
Understanding the Components of a Lathe Machine
To fully appreciate how a lathe machine works, it's essential to familiarize yourself with its key parts. Each component plays a significant role in the machine's operation and overall effectiveness.
1. Base
The base is the foundation of the lathe machine. It supports all other components, ensuring stability during operation. Typically made from cast iron, the base absorbs vibrations and provides a solid structure for accurate machining.
2. Headstock
The headstock houses the main drive mechanism, often containing the motor and the spindle. It controls the speed and direction of the workpiece's rotation. The headstock is designed for durability and precision, facilitating various machining tasks with ease.
3. Tailstock
The tailstock is located opposite the headstock and can be moved along the machine's bed. It provides support for longer workpieces and can also hold tools such as drills and taps. The tailstock enhances the lathe's versatility, allowing for additional operations like drilling.
4. Bed
The bed is a long, flat surface that holds the headstock and tailstock in alignment. It is crucial for maintaining accuracy in machining. The bed's construction must be rigorous enough to withstand constant wear from machining processes.
5. Carriage
The carriage moves along the bed and carries the cutting tool. It consists of several parts, including the cross slide and tool post, which allow for precise movements in various directions. The ability to control the carriage ensures that cuts are made accurately.
6. Tool Post
The tool post is attached to the carriage and holds the cutting tool in place. It can be adjusted for angle and height, providing flexibility in machining different workpieces. A secure tool post is essential for effective cutting.
7. Spindle
The spindle is the rotating component of the lathe that holds and drives the workpiece. Its high-speed rotation is what enables the lathe to perform various operations. The spindle must be precisely aligned and balanced to minimize vibrations.
8. Chuck
The chuck holds the workpiece in place as it rotates. There are various types of chucks, such as three-jaw and four-jaw chucks, each suited for different applications. Choosing the right chuck is vital for maintaining the integrity of the machining process.
9. Feed Mechanism
The feed mechanism controls the movement of the carriage and the speed of the cutting tool. It can be adjusted to accommodate different materials and machining requirements. Effective control of the feed mechanism is crucial for achieving the desired finish on the workpiece.
Types of Lathe Machines
There are several types of lathe machines, each designed for specific applications. Understanding these types can help you choose the right machine for your metal fabrication needs.
1. Engine Lathe
The engine lathe is one of the most common types used in workshops. It is highly versatile and suitable for a wide range of turning operations. Engine lathes can handle various sizes of workpieces, making them ideal for general machining tasks.
2. CNC Lathe
CNC lathes (Computer Numerical Control) automate the machining process, providing higher precision and repeatability. They are programmed using software to perform complex machining tasks with minimal human intervention, making them suitable for mass production.
3. Turret Lathe
Turret lathes are equipped with a rotating turret that holds multiple tools, allowing for quick tool changes. This feature makes them efficient for repetitive tasks, offering speed and productivity in machining operations.
4. Toolroom Lathe
Toolroom lathes are precision machines designed for making tools and dies. They offer high accuracy and are used for smaller production runs, where detailed work is required. Toolroom lathes provide a level of control that is ideal for custom fabrication.
5. Bench Lathe
Bench lathes are smaller, portable machines suitable for light machining tasks. They are often used in hobbyist applications or smaller workshops for tasks that do not require heavy-duty equipment.
Applications of Lathe Machines in Metal Fabrication
Lathe machines have a variety of applications in metal fabrication, showcasing their importance in the industry.
1. Turning
Turning is the primary operation performed on a lathe, involving the shaping of a workpiece by removing material as it rotates. This is used to create cylindrical shapes, including shafts, rods, and bolts.
2. Facing
Facing involves cutting the end of a workpiece to create a flat surface. This process is essential for ensuring that components fit together accurately in assemblies.
3. Drilling
Many lathe machines can perform drilling operations, which are necessary for creating holes in workpieces. The tailstock is often used to hold the drill bit, allowing for precise hole placement.
4. Tapping
Tapping is the process of cutting internal threads within holes. Lathe machines equipped with the appropriate tools can perform tapping operations efficiently, making them valuable for assembling threaded components.
5. Parting
Parting is a machining process used to cut off a part from the main workpiece. This operation is commonly used when creating separate components from a larger block of material.
Choosing the Right Lathe Machine for Your Business
Selecting the appropriate lathe machine is crucial for optimizing productivity and ensuring quality output. Here are some factors to consider:
- Type of Workpieces: Assess the size and material of the workpieces you will be machining. Different lathes accommodate varying sizes and materials.
- Production Volume: Consider whether you need a machine for low-volume custom work or high-volume production runs. CNC lathes are ideal for large quantities, while toolroom lathes are better for specialized tasks.
- Flexibility: If your projects vary significantly, a versatile engine lathe might be the best choice. For repetitive tasks, a turret lathe could save significant time.
- Budget: Establish your budget beforehand. Keep in mind that investing in higher-quality machinery can lead to long-term savings through increased efficiency and reduced maintenance costs.
- Space Availability: Ensure you have adequate space in your workshop for the lathe machine. Some machines may require specific setups or space considerations.
Maintenance of Lathe Machines
Proper maintenance of your lathe machine is essential to prolong its lifespan and ensure consistent performance. Here are some key maintenance practices:
1. Regular Cleaning
Cleaning the machine after use prevents metal shavings and debris from causing wear or interferences. Regular dusting and lubrication help maintain the machine's components.
2. Lubrication
Applying the appropriate lubricants to moving parts reduces friction and enhances performance. Ensure you follow the manufacturer's guidelines for the type and frequency of lubrication.
3. Check Alignments
Regularly check the alignments of the headstock, tailstock, and bed to ensure accuracy in machining. Misalignment can lead to poor cuts and premature wear of tools.
4. Tool Inspection
Periodically inspect cutting tools for wear or damage. Replacing dull tools is crucial for maintaining high-quality output and efficiency. Regular sharpening can extend the life of your tools.
Conclusion
The lathe machine with parts is a cornerstone of the metal fabrication industry, offering unmatched versatility and precision. Understanding its components, operation, and applications can greatly impact your business's efficiency and output quality. Whether you are a seasoned fabricator or a new entrant in the metalworking sphere, mastering the lathe machine will significantly enhance your capabilities. As you consider investing in this vital machinery, ensure you choose the right type based on your specific needs and maintain it diligently for optimal performance.
For further exploration of lathe machines and their parts, along with tailored solutions in metal fabrication, visit deepmould.net. Our team of experts is dedicated to providing the most effective tools and advice for all your machining requirements.