Unlocking the Potential of Plastic Injection Molding Manufacturing
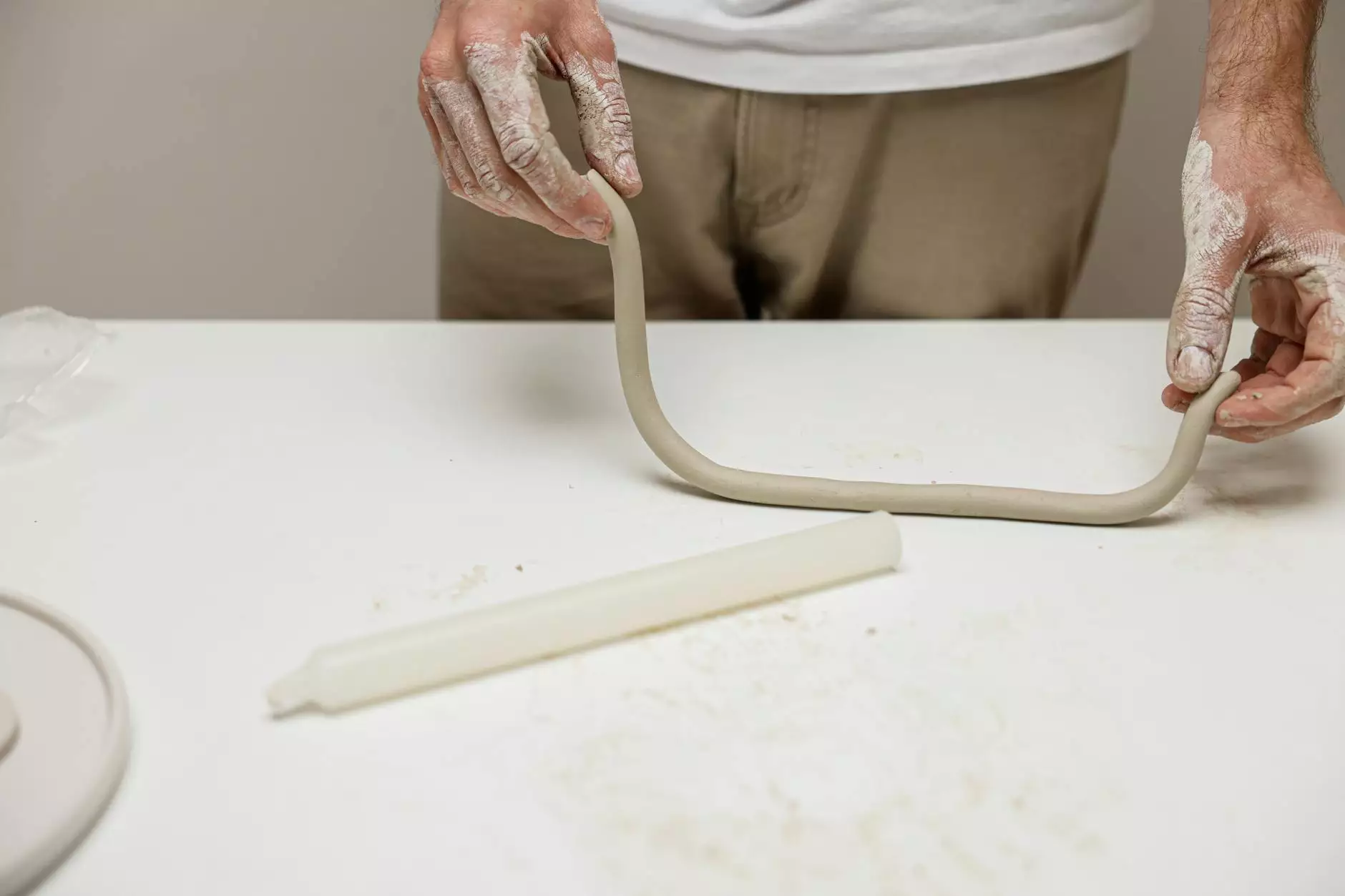
The world of plastic injection molding manufacturing is an intricate tapestry of technology, innovation, and creativity. This manufacturing process has revolutionized how we produce plastic parts and components, becoming an indispensable facet of numerous industries. In this article, we will dive deep into the intricacies of plastic injection molding, examining its processes, benefits, applications, and why it's essential for businesses like DeepMould.
What is Plastic Injection Molding Manufacturing?
Plastic injection molding manufacturing is a manufacturing process that involves the injection of molten plastic into a mold to create a specific product or component. The molds are designed to reflect the precise shape and dimensions of the final product. Once the plastic cools and solidifies, the mold is opened to release the finished product. This process is popular due to its ability to produce high volumes of consistent and complex shapes.
Detailed Overview of the Injection Molding Process
The plastic injection molding process can be broken down into several key stages:
1. Material Selection
The first step involves choosing the right type of plastic material suitable for the specific application. Different plastics exhibit varying properties, such as strength, flexibility, heat resistance, and environmental resistance.
2. Mold Design
Simulation and design software are utilized to create detailed 3D models of the mold. The design must consider product specifications, shrinkage rates, and cooling channels to ensure optimal performance and material flow.
3. Injection Phase
Molten plastic is injected into the mold at high pressures. The pressure helps ensure that the mold is filled completely, forming intricate shapes without any defects.
4. Cooling Phase
Once the mold is filled, the molten plastic needs time to cool and solidify. This stage is critical to achieving the structural integrity of the final product.
5. Ejection Phase
After sufficient cooling, the mold is opened, and the finished product is ejected. This phase may involve the use of ejector pins or plates, which ensure a smooth release.
6. Finishing Touches
Finally, the component may undergo trimming, finishing, or assembly depending on its intended use. This stage is crucial for ensuring the product meets design standards and customer expectations.
The Benefits of Plastic Injection Molding Manufacturing
Choosing plastic injection molding manufacturing has significant advantages that drive many businesses to adopt this method. Here are some of the most notable benefits:
- High Efficiency: Injection molding allows for rapid production rates, ideal for large-scale manufacturing.
- Consistent Quality: Once a mold is produced, every piece that follows can maintain high dimensional accuracy and consistency.
- Cost-Effective: Though the initial cost for mold creation can be significant, the overall cost per part decreases with high volumes.
- Material Variety: A diverse range of materials can be used, including thermoplastics, thermosetting plastics, and elastomers.
- Complex Geometries: Injection molding allows for the production of complex shapes and designs that would be challenging with other processing techniques.
- Reduced Waste: The process uses only the amount of plastic required, thus minimizing waste compared to other manufacturing methods.
Applications of Plastic Injection Molding
The applications of plastic injection molding manufacturing span across various industries, making it one of the most versatile manufacturing methods available today. Here are some key sectors that benefit from this process:
1. Automotive Industry
Automotive manufacturers utilize plastic injection molding to produce various components, such as dashboards, panels, and bumpers, ensuring durability and weight efficiency.
2. Consumer Electronics
Plastic housings for phones, laptops, and other electronics are often created through injection molding, combining aesthetics with functionality.
3. Medical Devices
The medical industry relies heavily on injection-molded parts for syringes, surgical instruments, and various equipment, often requiring stringent adherence to hygiene and safety standards.
4. Packaging Industry
Plastic injection molding provides solutions for creating a wide range of packaging products, ensuring durability and reducing material waste.
5. Household Products
From kitchen utensils to furniture components, plastic injection molding is instrumental in producing affordable and varied consumer goods.
Challenges in Plastic Injection Molding Manufacturing
Although plastic injection molding manufacturing is a highly efficient process, it does come with its own set of challenges. Understanding these can help businesses better navigate the complexities involved:
1. High Initial Costs
Developing molds can be a costly endeavor. The investment in both time and money may deter smaller companies from utilizing this method until they achieve significant production volumes.
2. Design Constraints
The design of the mold must consider the plastic's shrinkage properties, cooling rates, and intricacies of the part itself; failure to do so can lead to imperfections.
3. Material Limitations
Not all plastics are suitable for injection molding. Understanding the characteristics of different materials is crucial for ensuring product quality.
4. Environmental Concerns
While the process itself can generate minimal waste, the environmental implications of plastic usage are significant. Manufacturers must seek sustainable solutions through recycling and the use of biodegradable plastics.
The Future of Plastic Injection Molding Manufacturing
As we look toward the future, the landscape of plastic injection molding manufacturing is poised for exciting advancements. Emerging technologies such as automation, Industry 4.0 advancements, and the integration of machine learning are set to transform how manufacturers operate:
- Automation: Increased automation in the production process can enhance efficiency, reduce labor costs, and minimize human error.
- 3D Printing Integration: Combining injection molding with 3D printing techniques allows for rapid prototyping and feasible custom designs.
- Advanced Materials: Research into sustainable and high-performance materials continues to grow, opening doors to eco-friendlier practices.
- Data-Driven Decision Making: With the Internet of Things (IoT) and big data, manufacturers can analyze production efficiency and product quality in real time.
Choosing the Right Partner for Plastic Injection Molding
For businesses looking to leverage the benefits of plastic injection molding manufacturing, selecting the right manufacturing partner is crucial. Here are essential considerations when choosing the right provider:
1. Experience and Expertise
Partner with companies that have a proven track record and extensive experience in plastic injection molding. Knowledge in material science, mold design, and the latest technologies will greatly benefit your project.
2. Quality Assurance
Ensure your manufacturing partner implements stringent quality control processes. Certifications related to quality management systems, such as ISO 9001, are indicators of a company's commitment to delivering superior products.
3. Capacity and Scalability
Verify that the provider can meet your production volume requirements and can scale up operations as necessary. Flexibility in manufacturing can help you respond to market demands effectively.
4. Customer Support
Choose a company that values open communication and provides excellent customer service, ensuring you receive technical assistance and support throughout the production process.
Conclusion
In conclusion, plastic injection molding manufacturing is a pivotal technology in today’s competitive market, driving innovation across multiple industries. From its efficient production processes, material versatility, to its vast applications, this method has demonstrated its importance for modern business needs. As technological advancements shape the future, staying informed about the best practices and choosing the right manufacturing partner will position companies to not only thrive but lead in their respective markets. At DeepMould, we pride ourselves on delivering high-quality, precisely engineered solutions tailored to our client's specific needs. By embracing the advancements in plastic injection molding, your business can harness the potential of this remarkable manufacturing process.