Injection Molding Tooling: The Key to Quality Manufacturing
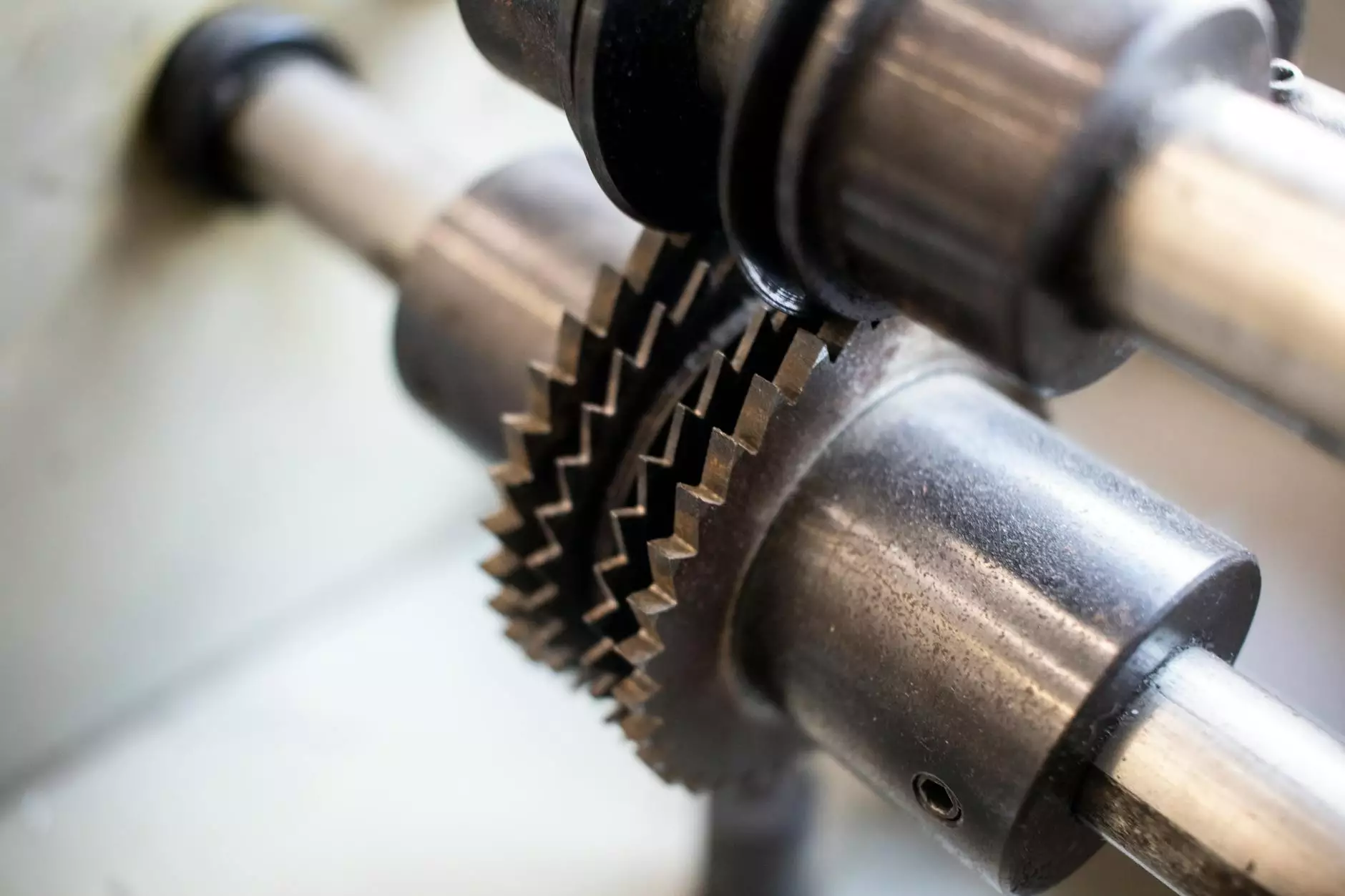
Injection molding tooling is a pivotal component in the manufacturing sector, especially for businesses specializing in metal fabrication. As industries evolve, the need for precision, efficiency, and cost-effectiveness has transformed how companies design and produce parts. In this comprehensive guide, we will delve into the intricacies of injection molding tooling, its processes, benefits, and the integral role it plays in achieving excellence in manufacturing.
The Science of Injection Molding Tooling
Injection molding is a manufacturing process whereby molten material is injected into a mold to create a desired shape. This highly versatile technique is predominantly used for metals and plastics, enabling the production of complex parts with tight tolerances. The tooling aspect refers to the tools and equipment involved in designing and creating the injection molds that shape the raw materials into final products.
Understanding Injection Mold Design
The design of injection molds is critical for ensuring that the final products meet quality standards. Key considerations in mold design include:
- Mold Geometry: The shape and complexity of the mold must align with the design specifications of the finished product.
- Material Selection: Choosing the right materials for both the mold and the product itself influences durability and performance.
- Cooling Channels: Efficient cooling is essential to minimize cycle time and maintain product quality.
- Gate Design: The gate is the entry point for the molten material, and its design affects the flow and fill of the mold.
Benefits of Injection Molding Tooling
The benefits of employing injection molding tooling in manufacturing are numerous and can significantly enhance business operations. Here are some of the most notable advantages:
- High Efficiency: Injection molding is known for its rapid production capabilities, allowing businesses to meet high demand without sacrificing quality.
- Cost-Effectiveness: Once the initial mold is created, the cost per part decreases dramatically, making it an economical choice for mass production.
- Precision and Consistency: Advanced tooling techniques ensure that each part produced is consistent with precise dimensions, which is crucial in industries requiring high accuracy.
- Material Versatility: Injection molding can process a wide range of materials, expanding the possibilities for product design and functionality.
The Injection Molding Process Explained
Understanding the step-by-step process of injection molding can provide insightful knowledge for those in the metal fabrication industry. Below is a simplified breakdown of the injection molding process:
1. Material Preparation
Raw materials, typically in pellet form, are dried and prepared for injection. This step is crucial, as moisture can lead to defects in the final product.
2. Melting the Material
The prepared pellets are fed into a heated chamber where they are melted into a viscous liquid state. The temperature must be carefully controlled to ensure optimal flow characteristics.
3. Injection into the Mold
Once the material is melted, it is injected into the mold at high pressure. The mold closes quickly to form the shape of the desired part.
4. Cooling and Solidification
After injection, the molten material is allowed to cool and solidify. This cooling phase is critical as it determines the dimensional accuracy and surface finish of the part.
5. Mold Opening and Part Removal
Once cooled, the mold opens, and the finished part is ejected. This process can occur quickly, allowing for rapid production cycles.
Quality Control in Injection Molding Tooling
Quality control is an essential aspect of the manufacturing process. To ensure that the injection molding tooling meets both industry standards and customer expectations, several methods can be implemented:
1. In-Process Testing
Monitoring the injection molding process in real-time allows manufacturers to catch defects early. Tools such as lasers and cameras can be used to inspect parts as they are produced.
2. Finished Product Inspections
After the manufacturing cycle, finished products should undergo thorough inspections to assess compliance with design specifications. This may include dimensional checks and quality assessments of the surface finish.
3. Statistical Quality Control (SQC)
Implementing SQC techniques helps manufacturers identify trends and variability in production, promoting consistent quality outcomes and efficient problem-solving.
Innovations in Injection Molding Tooling
The field of injection molding tooling is continuously evolving, driven by advancements in technology and materials. Some innovative developments include:
1. 3D Printing of Molds
3D printing technology is revolutionizing the creation of injection molds. It allows for rapid prototyping and the ability to produce complex geometries that were previously unachievable with traditional methods.
2. Smart Molding Technologies
Integrating IoT (Internet of Things) technologies enables real-time monitoring and data collection during the injection molding process, enhancing efficiency and reducing waste.
3. Biodegradable Materials
As sustainability becomes a priority, the use of biodegradable materials in injection molding is gaining traction. Manufacturers are now able to produce eco-friendly products while maintaining performance standards.
Conclusion: The Future of Injection Molding Tooling
In conclusion, injection molding tooling is a cornerstone of modern manufacturing, playing a crucial role in the success of metal fabrication and other industries. The benefits of this process, from efficiency to precision, are undeniable. As technology advances, the potential for innovation in tooling design and material use continues to expand, offering exciting opportunities for growth and improvement.
At DeepMould, we are dedicated to providing cutting-edge solutions in injection molding tooling. Our commitment to quality, precision, and innovation positions us as a leader in the industry. By continuously staying ahead of trends and technologies, we ensure that our clients receive the best products and services available.
Final Thoughts
For businesses looking to enhance their manufacturing processes, investing in high-quality injection molding tooling is essential. The combination of expert knowledge, advanced technology, and a focus on quality can elevate production outcomes and contribute to long-term success. Embrace the future of manufacturing with injection molding tooling that meets the demands of today and tomorrow.